Quality
OUR ONLY GOAL
100% QUALITY, 0% DEFECT.
OUR ONLY GOAL: 100% QUALITY, 0% DEFECT.
We are aware that our closures are part of a more complex packaging system, in which they must integrate perfectly eliminating any possible technical problem.
To the perfect functionality our customers add the demand for closures with increasingly sophisticated design, which require very complex painting processes.
The constant search for the best possible quality is carried out in Astro by applying the fundamental principles of Total Quality Management:
Focus on the customer
The actual level of quality we achieve is determined by our customers: their satisfaction is the only guarantee for the continuous improvement of the quality of our closures and services.
Involvement of staff
All our employees, at any level and regardless of role, are empowered and committed to deliver the best possible performance, being aware that this will affect the quality actually delivered to our customers. Through internal communication activities, at Astro everyone knows mission, vision and goals of the company.
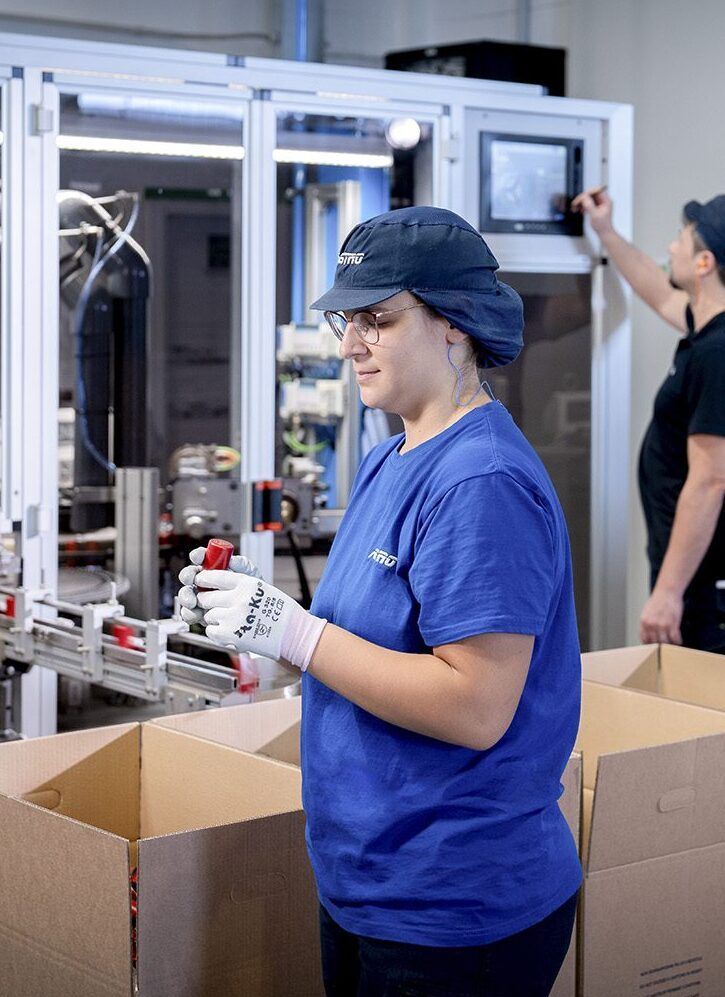

Integration of processes and organisational system according to Industry 4.0
Through the computerization of all internal processes and the search for maximum production automation, we set ourselves the goal of optimizing our production and the quality of our output to customers.
Digital numerical control
All the edging and assembly lines of the closures are equipped with cameras that check each single piece under different parameters (deformation, imperfection of the press, presence of the liner filler, etc.). Through a dedicated software, parts not complying with the required specifications are identified and discarded, thus eliminating non-conformity
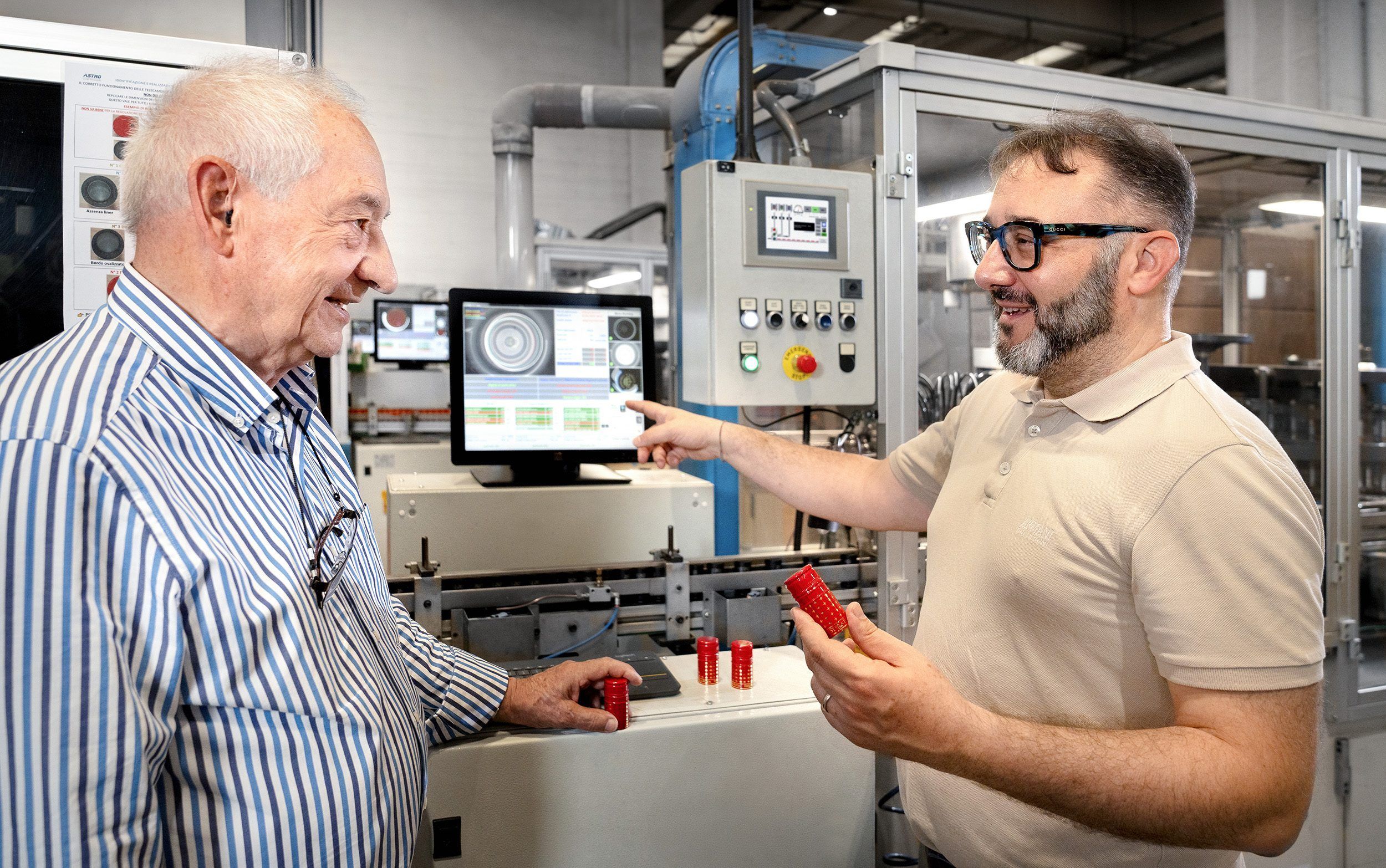
Continuous quality improvement
At Astro we believe in “continuous improvement”: we reward innovative and creative thinking, raising awareness and spreading the quality culture at all levels of the organization. Only in this way can we achieve and offer our customers the real quality excellence of our products and our services.
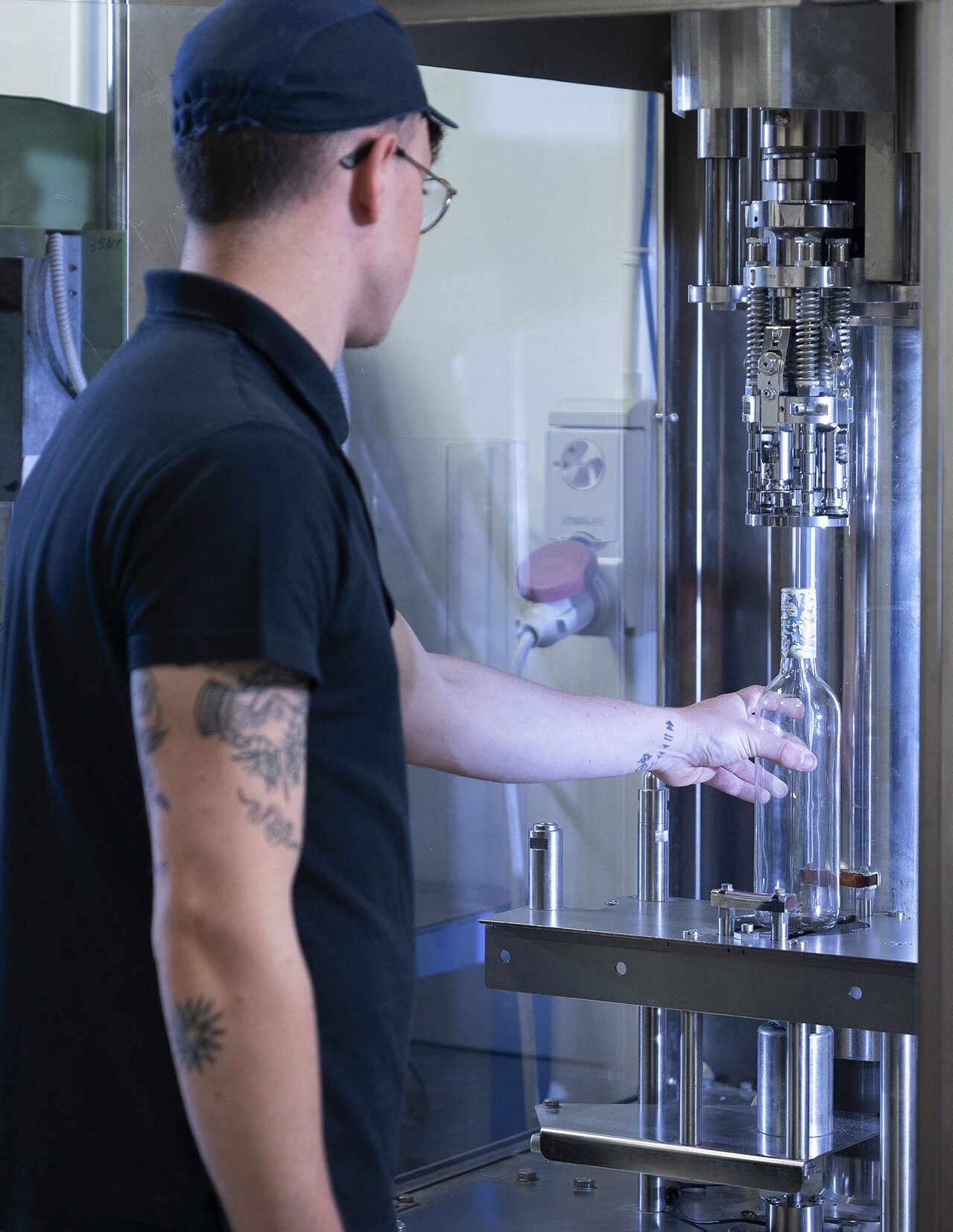
Internal Production Quality Control Laboratory
We have a highly qualified internal structure in terms of facilities and personnel, which perform sophisticated checks on the functionality of closures through special application simulations, using:
- Up to 12 capping machines, which reproduce the Capping of all types of capsules produced.
- Torque tester, for opening stress checks.
- Internal profiler, for profile and bottle finishing checks.
- Optical vision system.
- Oven and cold storage to simulate the aging process of the closures.
- Automatic industrial capping machine to simulate the application of closures in the bottling line.
We use Early Life Failure Rate (ELFR) procedures in the front-end and Real Time Control (RTC) in the back-end to monitor the quality of our closures and constantly check the reliability of processes during production.
Any suspected defect is analysed and, if confirmed, a corrective action plan is immediately implemented.
Certifications
As confirmation of the high standards of manifacturing and procedures that the company has achieved, Astro has obtained a series of important certifications:
Certification ISO 22000:2005
(possession of internal food safety management system requirements) for the design and production of dispensing and closing systems for food products, in aluminium and plastic. This standard guarantees the absolute safety of Astro closures for use with products intended for human consumption, thanks to the strict adoption of production processes, materials and staff training.
Certification of BRC Packaging standard
Developed by the British Retail Consortium (BRC), this standard certifies the absolute health and hygiene safety of packaging materials intended to come into contact with food.
To obtain this coveted certification, which has become an internationally recognized benchmark, Astro has adapted all its internal procedures to the needed requirements:
- Full traceability of production processes.
- Adoption of new internal safety protocols.
- Constant tests in the internal Quality Laboratory to ensure that no aftertaste or other dangerous chemicals are released to the content.
- Continuous checks at external laboratories accredited for the analysis of microparticles.
- GMP (Good Manufacturing Process) protocol for personnel (clothing, protections, training, etc.).
- Periodic audits by Italian certification bodies accredited BRC.
ISO 9001:2015 Certification
ISO 9001 is the reference standard for a company that intends to improve its services and operational processes with the aim of maximum customer satisfaction. Astro has obtained this certification as to the weighing of the finished and palletized product to ensure maximum transport safety, especially with regard to maritime containers, both for the carrier and for the final customer.
EcoVadis
It is one of the most important international sustainability rating platforms. It helps a company manage its ESG compliance and achieve defined sustainability goals, even across its entire value chain.
Ecovadis assigns a score to the performance of a company in relation to 4 macro-areas:
- Environment
- Labour practices and human rights
- Ethics
- Sustainable supply
SMETA
Sedex Members Ethical Trade Audit
It is the No. 1 social audit worldwide and verifies parameters such as safety, management of employees, availability of human rights protection policies and environmental policies within a company and its supply chain.
Read the occupational safety policy
Read the environment policy
Food quality and safety policy
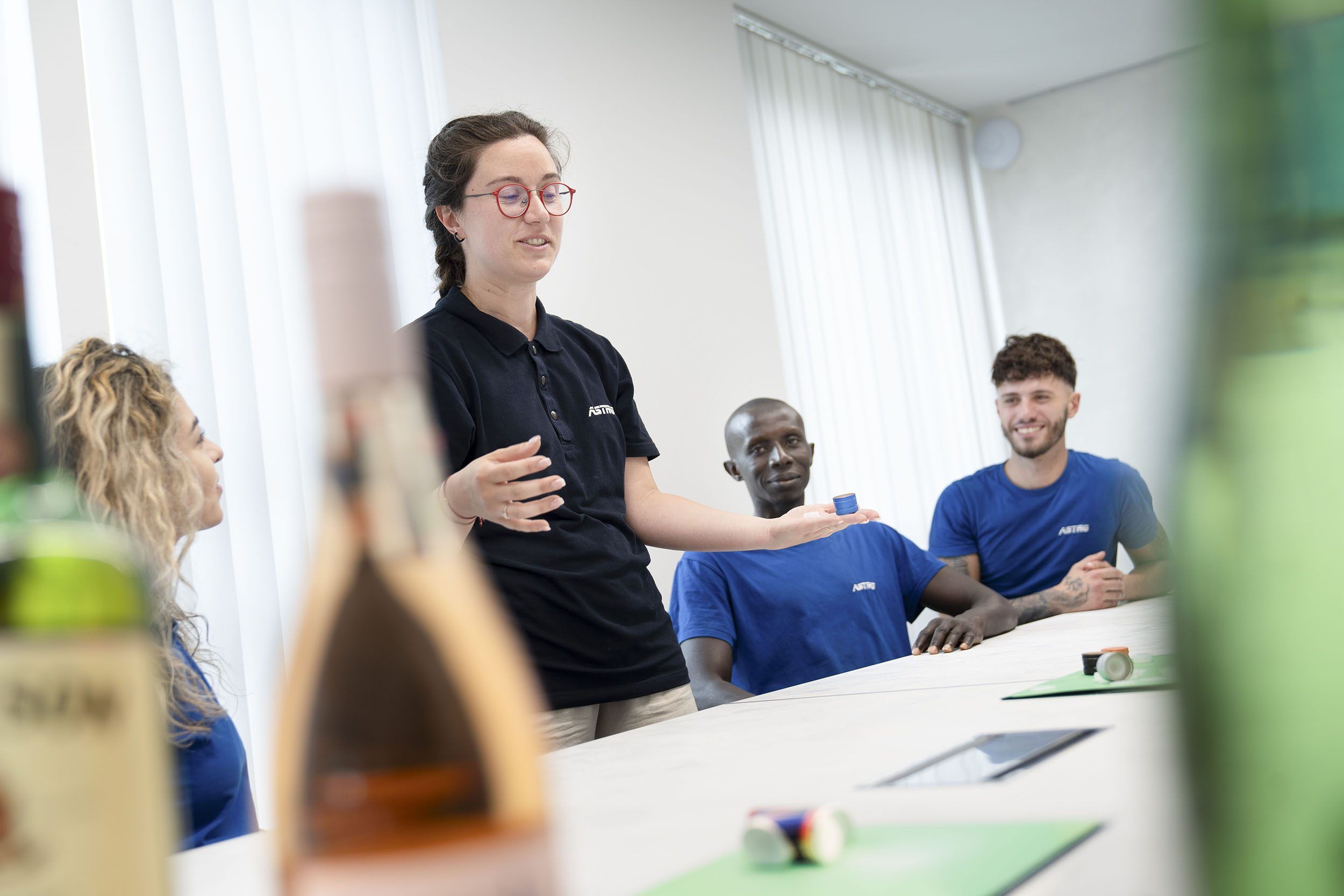